패러독스. 그리스 어원을 갖는 단어다. 여기서 파라(para)는 '차이가 있는' '구분된'의 의미다. 독스는 '의견'을 뜻하는 그리스어 독사(doxa)에서 왔다. 이 다른 의견이란 뜻이 훗날 파라독손(paradoxon)이란 라틴어가 되면서 역설 혹은 역설 상황이란 현재의 의미를 갖게 되었다고 한다.
일본기업의 혁신이 한참 속도를 내던 무렵 많은 글로벌 기업들이 이들 기업을 모방하고자 했다. 수천 개 기업에서 수만 명의 경영진이 공장을 견학했다. 자신들의 운영방식을 비밀로 하지도 않았다. 하지만 정작 모방에 성공한 기업은 드물다. 실망한 많은 기업들은 그들의 성공 비결이 문화란 것에 있다고 얼버무리고 만다.
과연 그럴까. 뭔가 놓친 것은 없을까. 누군가는 그렇다고 말한다. 많은 기업들이 두 가지 차이를 구분하지 못했기 때문이라 말한다. 바로 시스템과 도구를 구분하지 못한 것, 관행을 원리인 것처럼 착각하고 여기 매몰됐을 때 맞닥뜨리게 되는 병목, 바로 패러독스들이다.
우리가 시도하는 혁신은 대개 두 가지를 통해 구현된다. 그중 하나는 시스템이고, 다른 하나는 이것을 작동시키는 도구와 관행들이다.
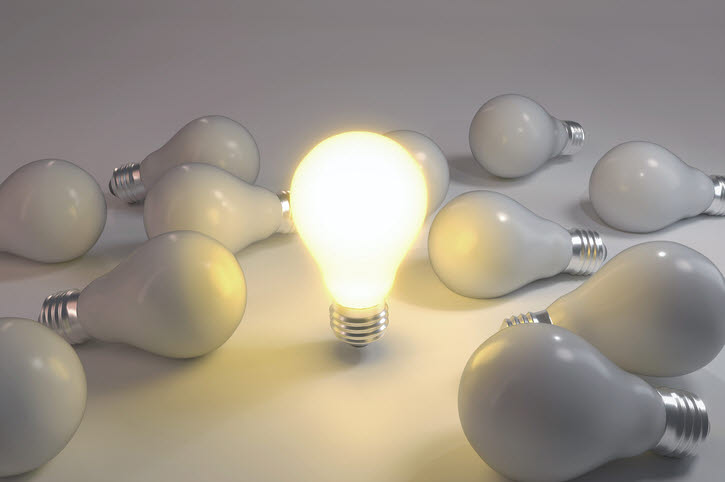
많은 최고 경영진이 방문한 공장에서 방문객들이 주목했던 것은 정작 칸반(Kanban) 카드나 품질관리서클 같은 도구와 관행들이었다. 하지만 정작 이것에 주목하면 할수록 시스템과 작동원리에서는 멀어진 셈이 되었다.
두 번째는 시스템의 연결과 흐름은 엄격하게 규정되지만 도구의 선택과 운영은 유연해야 한다는 상식과 다른 진실이었다.
20년도 더 지난 이야기이기는 하다. 이즈음 대개의 자동차 공장에서 앞좌석 설치란 이렇게 묘사되었다고 한다. 운반되어 온 자동차에 시트를 올린다. 상자에서 4개의 볼트를 가져온다. 이것을 토크 렌치(torque rench)로 조인다. 4개의 볼트를 조인 후 작업 완료 코드를 컴퓨터에 입력한다. 다음 차가 오기를 기다린다. 앞의 설명을 반복한다.
하지만 당시 어느 일본기업에서 앞좌석 조립 과정은 이랬다. 7단계 조립 과정은 55초에 끝나야 한다. 나사 조립은 앞쪽 볼트 먼저, 그다음 뒤쪽 순서로 진행한다. 이 조립 작업에 할당된 영역은 사각형으로 표시된다. 이 구역은 다시 1/10 단위로 표시되고 작업에 맞춰 진행되어야 한다. 즉 여섯 번째 칸에 서서 네 번째 작업을 하고 있다면 공정에 뒤처진 것을 단박에 알아차릴 수 있었다.
세 번째는 '대응책'과 '해결책'의 차이가 만드는 차이였다. 칸반 시스템이나 안돈 코드 같은 관행은 너무도 유용하지만 더 나은 접근 방식을 찾을 때까지의 임시 방편이란 것이었다. 아무리 유용한 도구나 관행이라도 변경되거나 심지어 제거될 수 있는 것들인 셈이었다. 이것은 문제에 '딩동'을 알리는 정답이 아닌 셈이었다.
누군가 어느 자동차 공장을 방문했다고 한다. 방문 전 그는 '무재고 관리'가 이곳 생산관리의 핵심이라고 들었던 터였다. 하지만 정작 부품 재고를 잔뜩 쌓아 놓은 걸 보게 된다. 그의 물음에 대한 답은 이랬다. “분명 이상적인 상태는 '재고 제로'죠. 하지만 그렇지 않아야 할 상황에서는 이게 대안이겠죠.”
카운터메저(대응책)와 솔루션(해결책)의 차이를 떠올려 보는 것만으로도 물음표보다는 느낌표가 붙는다.
![[박재민 교수의 펀한 기술경영]<300>시스템 패러독스](https://img.etnews.com/photonews/2202/1500440_20220208133509_007_0001.jpg)
박재민 건국대 기술경영학과 교수 jpark@konkuk.ac.kr